FAQ: Everything You Need to Know About Rubber 3D Printing
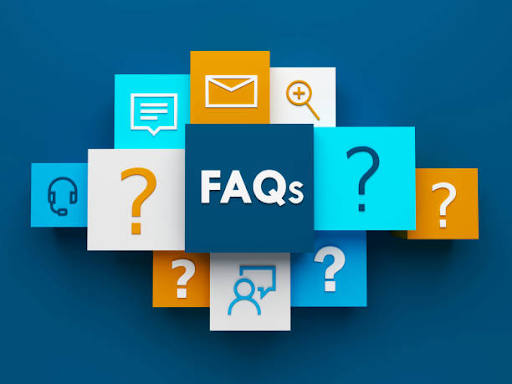
1. What is rubber 3D printing?
Rubber 3D printing is the process of creating flexible, rubber-like parts using additive manufacturing techniques. Instead of molding rubber into shape, parts are built layer by layer from digital designs using specialized elastomeric materials.
2. How does rubber 3D printing differ from traditional rubber manufacturing?
Unlike injection molding, which requires expensive tooling and long production times, 3D printing enables rapid prototyping, small-batch production, and complex designs without molds.
3. Can natural rubber be 3D printed?
No, natural rubber lacks the thermal properties required for direct 3D printing. Instead, thermoplastic elastomers like TPU and specialized photopolymers are used.
4. What materials are used for 3D printing rubber-like parts?
Common materials include thermoplastic polyurethane (TPU), high-rebound elastomers (SLA resins), and thermoplastic elastomers (TPE) via Freeform Injection Molding (FIM).
5. What are the main 3D printing technologies for rubber production?
- Multi Jet Fusion (MJF) – Uses TPU for durable, industrial applications.
- Stereolithography (SLA) – Produces soft, high-detail rubber-like parts.
- Freeform Injection Molding (FIM) – Combines 3D printed molds with traditional elastomers.
6. How does Multi Jet Fusion (MJF) work for printing rubber parts?
MJF fuses TPU powder using heat and chemical agents, producing flexible, strong, and chemically resistant parts with high resolution.
7. What are the benefits of using TPU in 3D printed rubber components?
TPU provides excellent wear resistance, flexibility, and durability, making it ideal for industrial seals, dampeners, and automotive applications.
8. How does stereolithography (SLA) work for rubber printing?
SLA cures liquid photopolymer resins with UV light, producing high-resolution elastomeric parts with a smooth finish.
9. What are the advantages of SLA for creating soft rubber parts?
SLA parts feature fine details, smooth surfaces, and excellent flexibility, making them suitable for medical devices and ergonomic grips.
10. How does Freeform Injection Molding (FIM) combine 3D printing with traditional rubber molding?
FIM 3D prints molds instead of parts, allowing manufacturers to use industry-standard rubbers like silicone and TPE.
11. What are the main advantages of 3D printed rubber over injection molding?
- No tooling costs
- Faster lead times
- Complex geometries
- Cost-effective for small batches
12. What industries use rubber 3D printing?
Industries include aerospace, automotive, medical, consumer goods, and industrial manufacturing.
13. How does 3D printing improve rubber prototyping?
It eliminates the need for molds, allowing for rapid iterations and functional testing.
14. Can 3D printing be used for manufacturing industrial rubber seals and gaskets?
Yes, TPU and SLA elastomers can produce custom, durable seals and gaskets on demand.
15. How is 3D printed rubber used in medical applications?
Applications include prosthetics, orthopedic insoles, and biocompatible wearables.
16. What are the benefits of 3D printed rubber in consumer products and footwear?
Custom shoe soles, ergonomic grips, and protective casings can be created without expensive molds.
17. How does 3D printing benefit automotive and aerospace rubber components?
It enables lightweight, custom rubber parts for seals, dampeners, and fluid connectors.
18. What design advantages does 3D printing offer for rubber parts?
Intricate lattice structures, variable wall thickness, and integrated textures.
19. Is 3D printed rubber as durable as traditionally manufactured rubber?
Yes, TPU-based prints offer comparable strength, but SLA resins may have lower tear resistance.
20. How does the cost of 3D printing rubber compare to injection molding?
For small runs, 3D printing is cheaper, but injection molding is more cost-effective for large-scale production.
21. What are the main limitations of 3D printed rubber?
- Limited material selection
- Lower tear resistance in some prints
- Size constraints
22. Can 3D printed rubber match the flexibility and softness of traditional rubber?
Yes, but only specific materials like SLA high-rebound elastomers achieve softer rubber-like properties.
23. How does 3D printing reduce waste compared to traditional rubber manufacturing?
Additive manufacturing only uses necessary material, eliminating excess waste from molds.
24. What is the Shore hardness scale, and how does it apply to 3D printed rubber?
It measures material softness; 3D printed elastomers range from Shore 30A to 90A.
25. Can 3D printing be used to make rubber overmolded parts?
Yes, hybrid techniques allow 3D printed molds for overmolding processes.
26. What are the sustainability benefits of rubber 3D printing?
Less material waste, on-demand production, and reduced energy consumption.
27. Are 3D printed rubber parts biocompatible?
Some TPU and SLA elastomers are FDA-approved for medical use.
28. What are the future advancements in rubber 3D printing?
New elastomers, faster printers, and improved durability.
29. Can 3D printed rubber parts be mass-produced?
For small-to-medium runs, yes, but injection molding is still more efficient for high-volume production.
30. Where can I get custom 3D printed rubber parts?
RapidMade specializes in high-quality rubber 3D printing for industrial and commercial applications. Visit www.rapidmade.com to get started!