The Art and Science of Precision Machining: Insights and Innovations
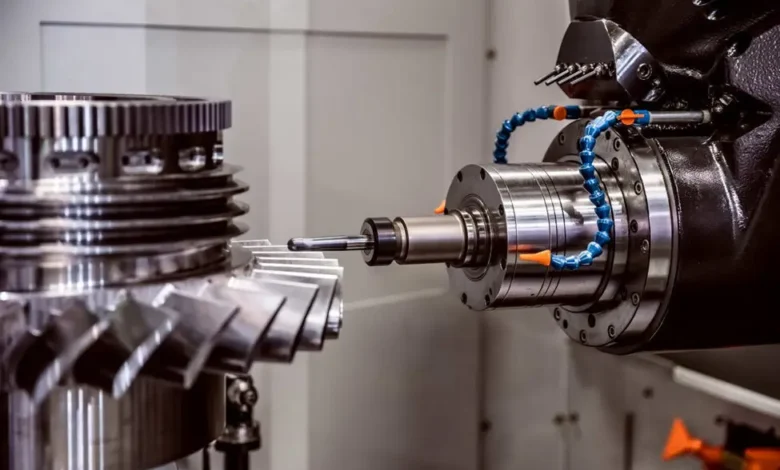
Table of Contents
- Introduction to Precision Machining
- The Role of Technology in Precision Machining
- Materials Used in Precision Machining
- Standard Techniques in Precision Machining
- Challenges and Solutions in Precision Machining
- The Future of Precision Machining
- Insights from Industry Experts
- Conclusion
Introduction to Precision Machining
Precision machining is a pillar of modern industry, integral to manufacturing processes across many sectors, including aerospace, automotive, and healthcare. This art of sculpting raw materials into intricate, precise components necessitates a profound understanding of both mechanical processes and technical expertise. A tool and die company is often at the heart of these advancements, blending innovation with tradition to achieve unparalleled precision. Precision machining has evolved from manual craftsmanship to sophisticated computer-controlled operations driven by a relentless pursuit of accuracy and efficiency. This evolution aligns with modern engineering demands and consumer expectations. It is impossible to overestimate the significance of precision machining since it fosters industrial expansion and makes technical breakthroughs that impact our world possible.
The Role of Technology in Precision Machining
The infusion of technology into precision machining has been a game changer. Innovations like computer-aided design (CAD) software and computer numerical control (CNC) machines have completely changed how machining approaches. These technological tools bring multiple benefits, such as enhanced precision, reduced human error, and significant production speed and reliability improvements. The role of technology in manufacturing is pivotal, serving as a catalyst for these changes and making complex operations easier to execute and monitor.
Furthermore, these advancements have allowed manufacturers to experiment with complex geometries and intricate parts that were previously deemed impossible. Maintaining efficiency and pushing the limits of design and application innovation require these skills.
Materials Used in Precision Machining
Material selection is essential in precision machining since it directly impacts the final product’s performance, robustness, and cost-effectiveness. Predominant materials include metals like aluminum, steel, and titanium, favored for their strength and resilience. Plastics and composites are also popular choices, especially for applications where weight reduction is critical. The material selection process considers durability, application requirements, and the complexity of the manufacturing process involved.
As technology evolves, so do the materials used, leading to new composites that offer enhanced properties such as excellent thermal stability and improved tensile strength. These advancements not only expand the possibilities in manufacturing but also help industries meet the stringent demands of a competitive market.
Standard Techniques in Precision Machining
Precision machining encompasses a variety of techniques, each suited to different manufacturing needs and specifications. Milling, turning, and drilling are among the most widely used methods, offering unique benefits and applications. For example, milling is ideal for creating complex surfaces and features, while turning is perfect for producing components with cylindrical features. Each technique is selected based on project requirements, material properties, and desired outcomes.
These procedures involve a lot more than just cutting materials; they encompass a detailed process, including planning, programming, and execution, which requires both skill and precision to accomplish effectively.
Read Also: Apple Intelligence: Your Personalized Tech Assistant
Challenges and Solutions in Precision Machining
While precision machining holds numerous advantages, it also presents several challenges. Material waste, ensuring high precision amidst complex operations, and managing costs are common hurdles manufacturers must navigate. However, innovative solutions and strategic approaches, such as adopting lean manufacturing principles and utilizing advanced CNC programming techniques, have been pivotal in overcoming these challenges. Real-time quality control and process optimization are also critical elements that help manufacturers maintain high standards while minimizing costs.
Many industry leaders have successfully employed these strategies to optimize their processes, reduce wastage, and improve output quality, turning challenges into opportunities for improvement.
The Future of Precision Machining
The prospects of new technologies brightly illuminate the future of precision machining. The profession is about to undergo a revolution thanks to automation, AI, and machine learning, which promise previously unheard-of levels of accuracy, efficiency, and personalization. These technological innovations not only streamline manufacturing operations but also pave the way for breakthroughs in complex component design and performance optimization.
With such exciting developments on the horizon, businesses in the machining industry are poised to redefine the standards of quality and innovation, ensuring that precision machining remains a cornerstone of global industrial advancement.
Insights from Industry Experts
Industry experts provide invaluable perspectives on the current landscape of precision machining and its future directions. They stress the crucial importance of continuing to learn and adapt in a changing field. Insights from industry platforms, such as industry insights and trends, reinforce the notion that embracing new technologies and methodologies is essential for driving innovation and maintaining competitiveness.
These insights often serve as a guide for professionals who aim to harness cutting-edge technologies and use them to gain strategic advantages.
Conclusion
Precision machining is a dynamic field that continues to expand the boundaries of what is possible in modern manufacturing and engineering. Integrating technology alongside innovative materials and methodologies ensures that precision machining will remain at the forefront of industrial and technological advancements. Achieving excellence in precise manufacturing and opening up new opportunities will depend on embracing change and encouraging innovation as the sector develops.