How to Design and Implement Aluminum Enclosures for Electronics: Factors to Consider for Long-Term Reliability
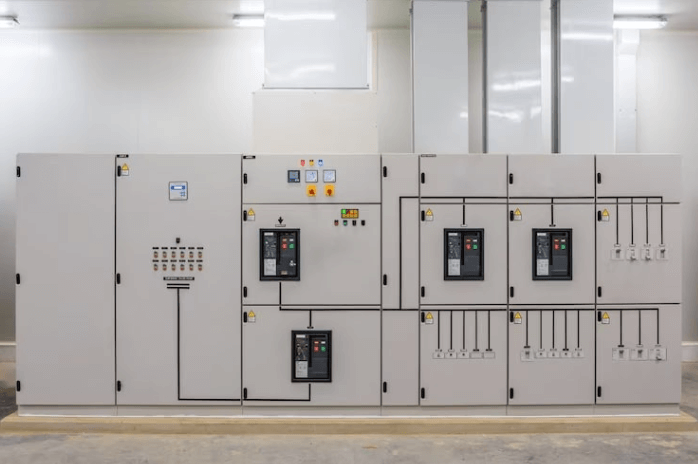
Electronic devices and instruments rely heavily on their enclosures to provide protection, thermal management, and durability.
Aluminum is a popular choice for enclosures due to its excellent properties such as lightweight, corrosion resistance, and effective heat dissipation.
Designing and implementing aluminum enclosures requires careful consideration of various factors to ensure long-term reliability and optimal performance. This article explores key aspects to keep in mind when designing and implementing aluminum enclosures for electronics.
Understanding the Importance of Aluminum Enclosures
Why Choose Aluminum?
Aluminum is favored for electronic enclosures for several compelling reasons:
1. Strength and Lightweight: Aluminum offers a good strength-to-weight ratio, making it suitable for both lightweight portable devices and robust industrial applications.
2. Corrosion Resistance: Aluminum naturally forms a protective oxide layer, enhancing its resistance to corrosion in various environments.
3. Heat Dissipation: Aluminum efficiently conducts heat away from electronic components, helping to maintain optimal operating temperatures.
4. Electromagnetic Shielding: Aluminum electronics enclosures can provide effective electromagnetic interference (EMI) shielding, crucial for sensitive electronics.
Design Considerations for Aluminum Enclosures
Mechanical Design
Enclosure Type: Choose between extruded, die-cast, or fabricated aluminum enclosures based on the application’s mechanical requirements and production volume.
Gasketing and Sealing: Ensure proper sealing to protect against dust, moisture, and other environmental factors. Consider IP ratings for ingress protection.
Mounting Options: Incorporate provisions for PCB mounting, connectors, and other internal components to facilitate assembly and serviceability.
Thermal Management
Heat Sink Design: Utilize the enclosure’s surface area for effective heat dissipation. Consider adding fins or integrating thermal pads to enhance cooling efficiency.
Ventilation and Airflow: Plan ventilation slots or fans to promote airflow inside the enclosure, especially for devices generating significant heat.
EMI/RFI Shielding
Material Thickness: Optimize aluminum thickness to achieve desired shielding effectiveness against electromagnetic interference (EMI) and radio frequency interference (RFI).
Design for Grounding: Ensure proper grounding of the enclosure and components to mitigate EMI/RFI issues. Use conductive gaskets or coatings where necessary.
Material Selection and Finishing
Alloy Selection
Alloy Properties: Choose aluminum alloys (e.g., 6061, 6063) based on mechanical strength, corrosion resistance, and thermal conductivity requirements.
Surface Treatment: Apply finishes such as anodizing or powder coating to enhance corrosion resistance, aesthetics, and EMI shielding capabilities.
Environmental Considerations
Durability and Reliability
Environmental Testing: Subject prototypes to environmental stress tests (e.g., temperature cycling, humidity) to validate durability and reliability under real-world conditions.
Lifecycle Considerations: Assess the expected lifecycle of the product and ensure the enclosure materials and design can withstand prolonged use and potential impacts.
Manufacturing and Assembly
Design for Manufacturing (DFM)
Simplified Designs: Collaborate with manufacturers early in the design phase to optimize for cost-effective production processes such as CNC machining or injection molding.
Tooling and Prototyping: Invest in prototype iterations to validate design, fit, and function before full-scale production.
Assembly and Serviceability
- Accessibility: Design for ease of assembly and maintenance, considering access to internal components, fastening methods, and modular designs where applicable.
- Serviceability: Incorporate features like removable panels or access points for troubleshooting and component replacement without compromising enclosure integrity.
Conclusion
Designing and implementing aluminum enclosures for electronics requires a systematic approach that balances mechanical integrity, thermal management, EMI shielding, material selection, and environmental considerations.
By understanding these key factors and integrating them into the design process, engineers can enhance the reliability, performance, and longevity of electronic devices.
Whether for consumer electronics, industrial equipment, or specialized instruments, aluminum enclosures offer a versatile solution to protect and optimize the functionality of electronic assemblies.
In summary, the successful integration of aluminum enclosures involves a holistic approach from initial design concept through to manufacturing and deployment. By focusing on these critical factors, designers and engineers can ensure that their electronic devices not only meet but exceed performance expectations in terms of reliability and longevity.